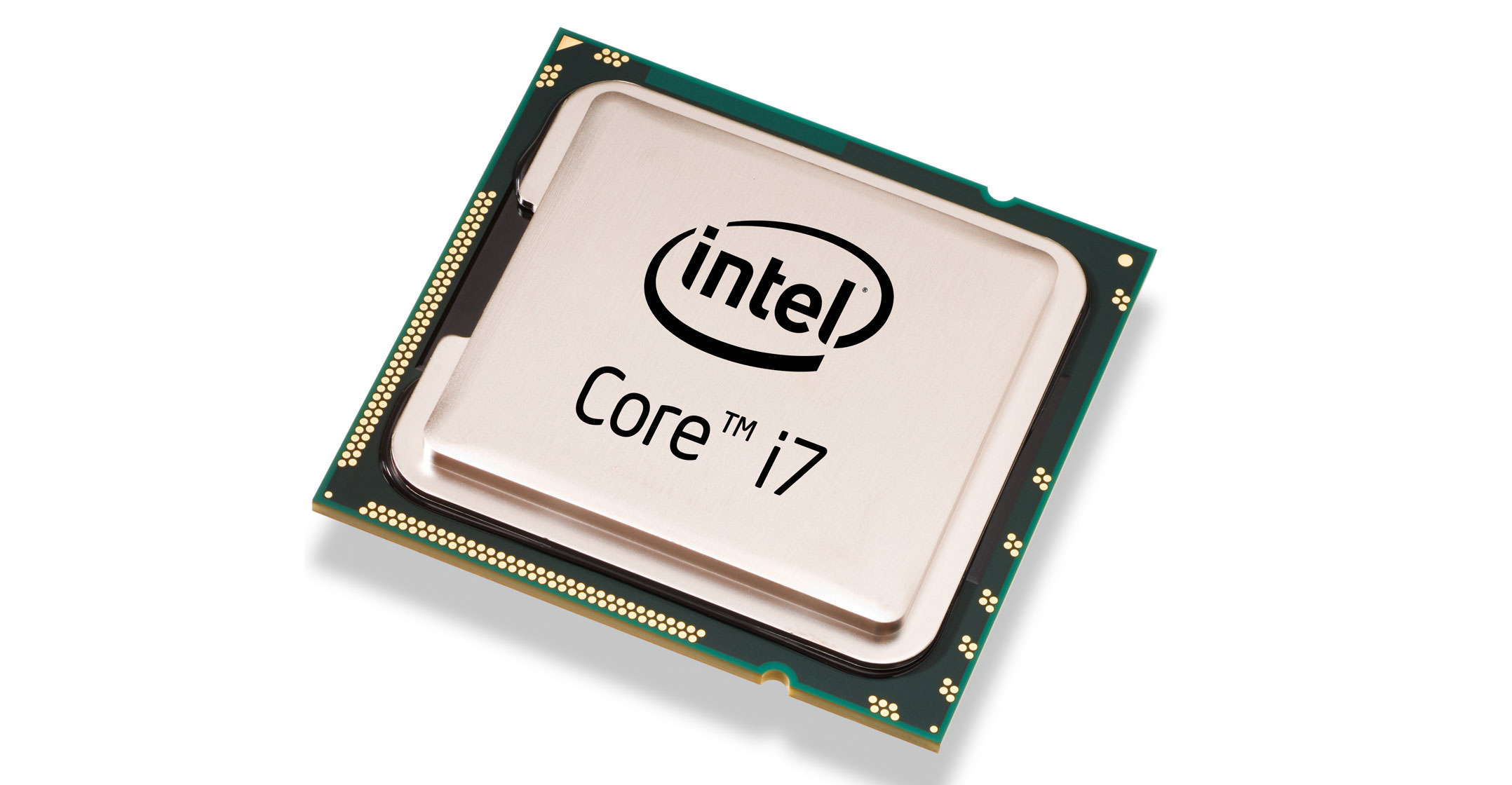
Samsung Electronics rose the most in almost 10 months after Intel was said to be considering asking the South Korean giant and Taiwan Semiconductor Manufacturing Co (TSMC) to make some of its most sophisticated chips, a major departure for the Silicon Valley pioneer.
After successive delays in its chip fabrication processes, Santa Clara, California-based Intel has yet to make a final decision less than two weeks ahead of a scheduled announcement of its plans, according to people familiar with the deliberations. Any components that Intel might source from Taiwan wouldn’t come to market until 2023 at the earliest and would be based on established manufacturing processes already in use by other TSMC customers, said the people, asking not to be identified because the plans are private.
Intel is still holding out hope for last-minute improvements in its own production capabilities. Talks with Samsung, whose foundry capabilities trail TSMC’s, are at a more preliminary stage, the people said. TSMC and Samsung representatives declined to comment. An Intel spokesman referred to previous comments by Bob Swan, the company’s CEO.
Swan has promised investors he’ll set out his plans for outsourcing and get Intel’s production technology back on track when the company reports earnings on 21 January. The world’s best-known chip maker has historically led the industry in advanced manufacturing techniques, essential for maintaining the pace of performance increases in modern semiconductors. But the company has suffered years-long delays that have put it behind competitors that design their own chips and contract TSMC to do the manufacturing.
Modular approach
Intel shares slid 1% Friday. Samsung soared more than 9% to an all-time high in Seoul on Monday, the biggest gain since March on an intraday basis. TSMC, which is already operating at full throttle and may not have spare capacity in the short run, stood largely unchanged in Taipei after a seven-day wining streak.
Under the leadership of Jim Keller, Intel designers moved to a more modular approach to creating microprocessors. This provides more flexibility to either make chips in-house or outsource the work. But Keller left Intel last year, and rivals, such as AMD and Apple, have forged ahead with their own capable designs and TSMC’s more advanced production technology. That has put Intel under intense competitive pressure and forced it to make last-minute changes to product road maps, complicating its decision making, the people said.
“We have another great line-up of products in 2022, and I’m increasingly confident in the leadership our 2023 products will deliver on either Intel 7-nanometre or external foundry processes, or a combination of both,” Swan said on a conference call in October. Semiconductor manufacturing processes are measured in nanometres, with ever more microscopically small transistors crammed onto silicon wafers with each new iteration.
At subsequent investor conferences, Swan explained that the timing of his decision is driven by the need to order chip-making equipment to make sure he has enough factory capacity or give a partner enough of a heads-up to make similar preparations. Being able to predictably deliver leading products to customers on time, at the right cost, will determine how much outsourcing Intel uses, he said.
TSMC, the largest maker of semiconductors for other companies, is preparing to offer Intel chips manufactured using a 4nm process, with initial testing using an older 5nm process, according to the people. The company has said it will make test production of 4nm chips available in the fourth quarter of 2021 and volume shipments the following year.
The Taiwanese company expects to have a new facility in Baoshan operational by the end of this year, which can be converted to production for Intel if required, one of the people said. TSMC executives previously said the new Baoshan unit would house a research center with 8 000 engineers.
Activist investor Dan Loeb has also given voice to shareholder discontent with what’s perceived to be Intel’s technological stagnation, urging that the company make aggressive strategic changes.
While Intel has outsourced production of lower-end chips before, it has kept the manufacturing of its best semiconductors in-house, considering it a competitive strength. Its engineers have historically tailored their designs to the company’s manufacturing processes, making a shift to outsourcing of flagship products unthinkable in the past.
Scale
As the provider of 80% of PC and server processors globally, Intel produces hundreds of millions of chips each year. That scale dictates that any potential supplier must create new capacity to accommodate Intel.
In July, the company said its 7nm production would arrive a year later than previously planned. That followed a three-year delay in the introduction of the preceding 10nm generation, which is only reaching mainstream use now. Those holdups have allowed TSMC and Samsung to lay claim to better technology for the first time, with TSMC already producing 5nm silicon at volume for Apple and others. That timeline suggests other customers could move to better TSMC production before Intel would.

Intel’s strategic shifts are happening at a time of booming demand as well as technological change in the chip industry. The traditional method of improving performance by shrinking and cramming more transistors into each package is being supplanted by more sophisticated techniques that include stacking processor and memory components into single chips and the introduction of more tailored designs for tasks like artificial intelligence.
AMD and others have partially mitigated the risk of manufacturing advances not proceeding at the expected pace by segmenting their designs, allowing the assembly of various component parts of the processor in stages. Intel has said it’s also moving toward that modular approach. — Reported by Ian King and Debby Wu, (c) 2020 Bloomberg LP