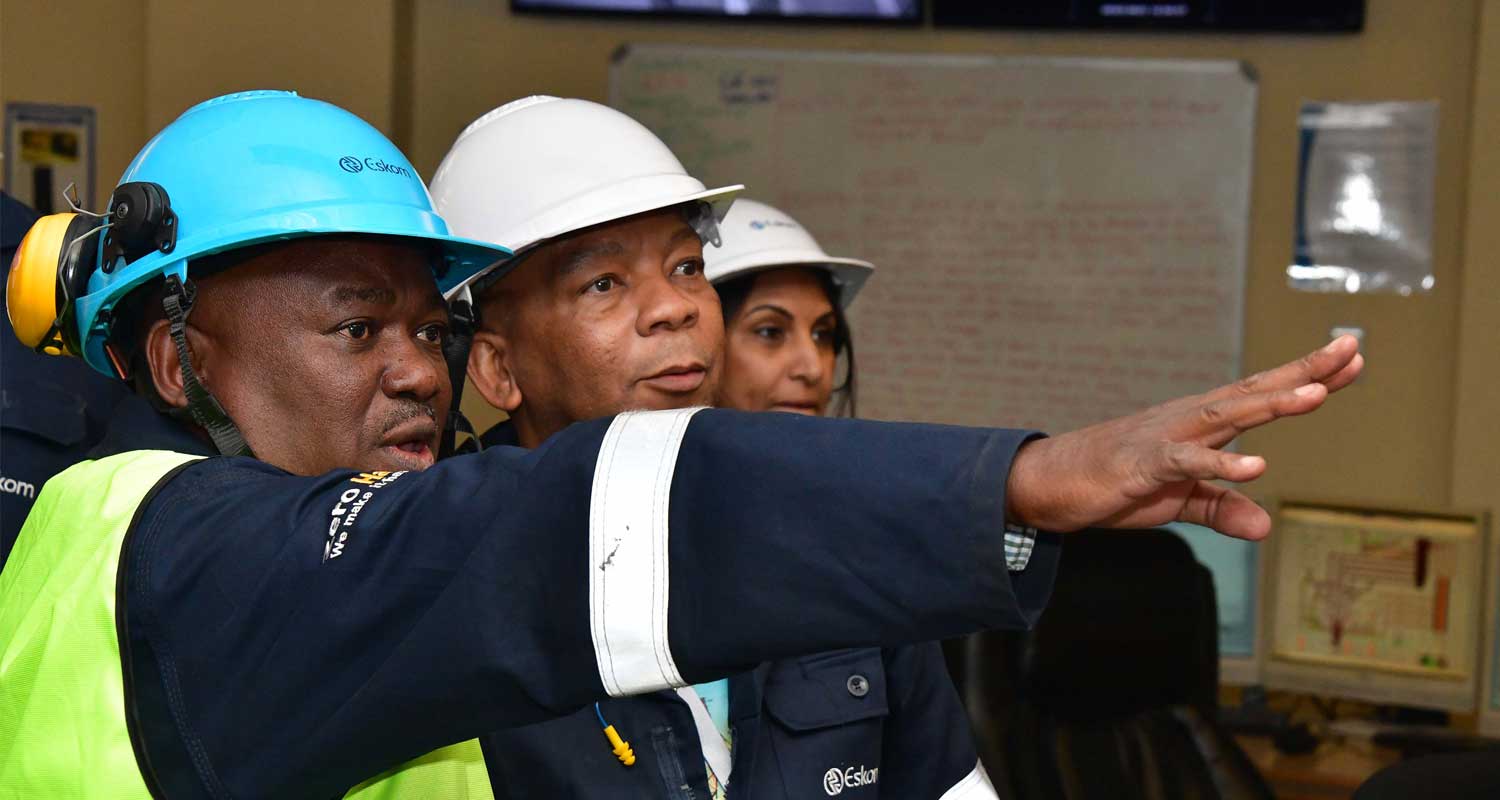
In a positive move to improve Eskom’s performance, government is making overtures to power plant original equipment manufacturers (OEMs) to become more involved in the running of the utility and the technical maintenance of its ageing equipment.
In February, national treasury announced it had appointed Germany’s VGBE Energy to investigate the operations of Eskom’s coal fleet, an assessment due to be concluded this month.
Treasury said the outcome of the assessment could mean putting in place a concession model, which would see OEMs brought in to improve the energy availability factor and performance of Eskom’s coal-fired power plants.
This is seen as critical to solving the electricity crisis and ending load shedding and, at a webinar on Thursday, the role of OEMs in turning around the current crisis and ending, or at least reducing, load shedding was explored in some detail.
The problems facing Eskom are myriad, ranging from poor maintenance to corruption and even alleged sabotage. Eskom itself has stated that boiler-tube failures are the main culprits for load shedding, and the rate at which these failures occur has been rising. Eskom set itself a target of one tube failure per unit per year but, as of 2021, was averaging 2.3 failures a year.
Poor maintenance
This number has been rising since then, with 2022 by far the worst year of load shedding ever. Last December, GroundUp reported that Eskom’s coal fleet was operating at just 40% of its installed capacity, far short of its stated target of 75%.
Part of the problem lies in maintenance. Perhaps more alarmingly, when maintenance is carried out, it doesn’t always meet standards and the units fail anyway, the publication reported. But the contributors to Thursday’s webinar certainly believe OEMs can help Eskom solve some of its problems.
Siemens Energy Southern Africa MD Thabo Molekoa listed a number of ways Eskom could augment the performance of its coal plants, including long-term service agreements where relationships are cemented. This also offers predictability and helps retain skills and expertise, he said.
“Long-term planning is vital. Some of Eskom’s turbines have legacy technology systems with limited spares or support, and therefore are hard to maintain. But local manufacturing can step into that breach and ensure that procurement for assets is maintained. Repairs and parts can be supplied locally.”
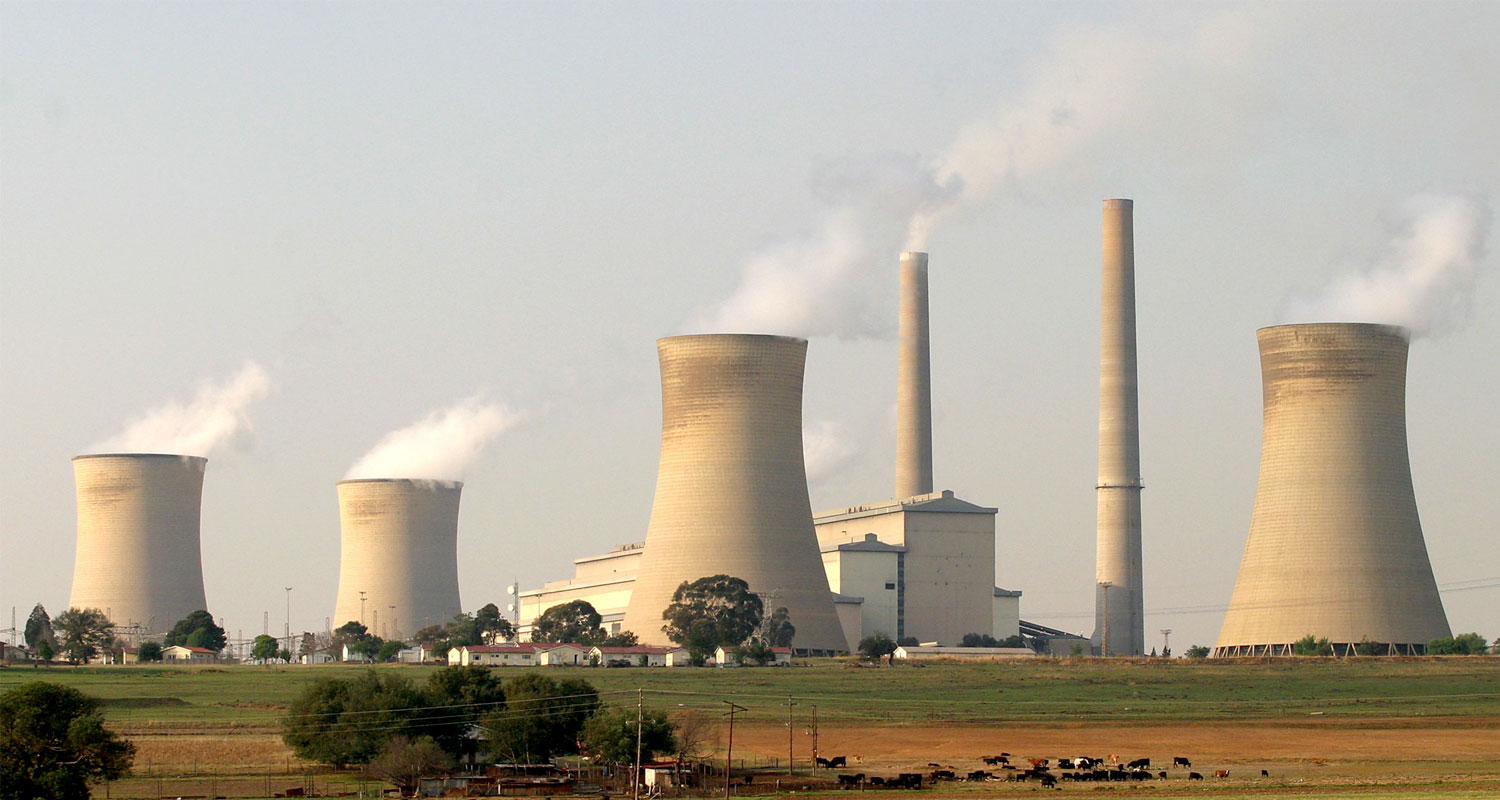
Ewart Snyman, who started his career as a systems engineer at the Kriel power station and who is now regional engineering manager at John Thompson (a division of multinational electrical firm Actom) said an often-overlooked fact is that most of Eskom’s coal stations were built in the 1970s and 1980s and that since then the market for these kinds of boilers has dropped significantly.
“Many of the companies that used to support Eskom no longer even own the technology. Actom does welding maintenance on power stations – Eskom’s performance would be much worse without OEMs. But there is so much more that could be done,” Snyman said.
“We need availability of materials. The current contracts do not include the provision of spares, and Eskom often struggles to source materials, so outage times are extended as the required spares are not available on time for boiler maintenance to take place.
“Also, because of the focus on avoiding load shedding, the emphasis is on finding the quickest solution in the short term, so ‘best practice’ is being neglected. The immense pressure on everyone at the power stations changes how things are being done, but we have the expertise to weather the storm,” he said.
One of the problems is just slack supply-chain management. We have allowed ourselves to become ill-disciplined
The provision of spares and strict inventory control is basic to the smooth functioning of the aged plants. “One of the problems is not even corruption but just slack supply-chain management,” according to Eskom generation engineering GM Thomas Conradie. “We have allowed ourselves to become ill-disciplined.
“We often find, for instance, that a tender we have accepted is suddenly unavailable as the date for delivery approaches, and then we have to start the whole process again. But we are using the original manufacturers now as far as possible and avoiding intermediaries.”
Many of the participants in the webinar were upbeat in their assessment of how Eskom could immediately raise its game, and convener, energy expert Chris Yelland, said it makes sense for OEMs to be given specific areas to handle, with longer-term contracts, along the lines of the agreement between Sasol and Air Liquide, for instance, which supplies oxygen to Sasol.
‘Are you ready?’
According to electricity minister Kgosientsho Ramokgopa’s adviser, Silas Zimu, Eskom is reviewing how to make more use of OEMs in its power plants.
“The minister knows it all starts with electricity, and the economy follows; there has always been private participation. But now we are repurposing, we need to work together. We are saying to OEMs: are you ready? Come and be with us now.” — © 2023 NewsCentral Media