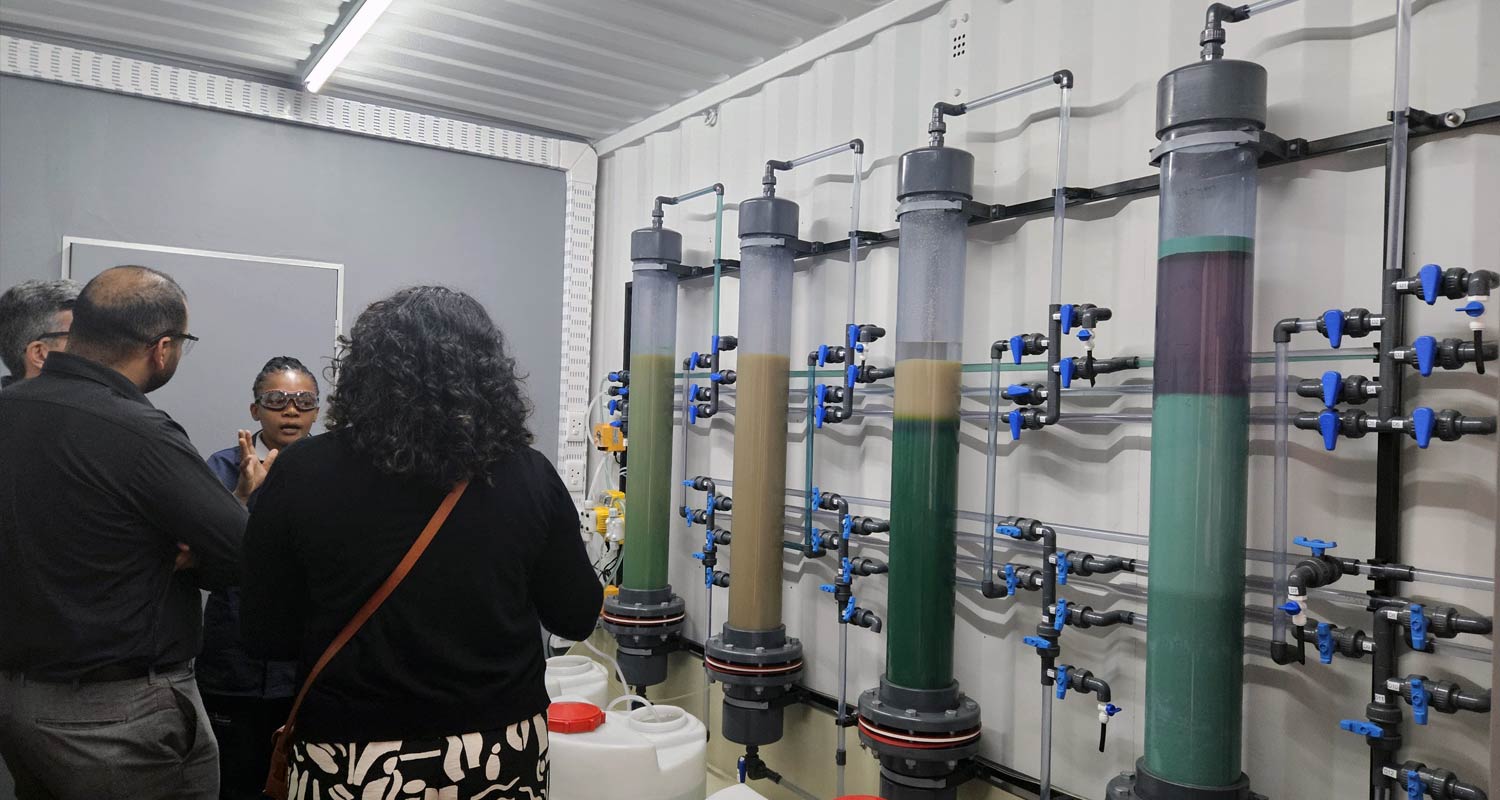
Lithium-ion batteries have become integral to everyday life, especially in South Africa, which, until March this year, had been subjected to severe load shedding.
Yet the ability for consumers to recycle the lithium batteries they’ve bought to help them through the rolling blackouts, once they reached their end of life, has been constrained by a lack of recycling facilities in South Africa.
Johannesburg-based Cwenga Lib is hoping to change that with a new processing facility in Germiston. The company declined to disclose how much it invested in the plant.
The journey of a lithium-ion battery at the facility begins with collection. Batteries are gathered through various means, including partnerships with informal collectors, helping address waste management issues across Gauteng.
Once collected, the batteries undergo shredding, which exposes the valuable metal-containing black mass at their core. From there, the black mass enters a proprietary hydrometallurgical process, where a blend of food-safe chemicals is used to leach out metals such as lithium, manganese, nickel and cobalt.
Unlike traditional methods that rely on pyrometallurgy and high temperatures, Cwenga Lib’s facility operates at room temperature, making it safer for operators and more feasible in the South African context.
Purified and separated
The extracted metals are then purified and separated using a series of ion-exchange columns, employing technology akin to chromatography. This method allows it to recover valuable materials while minimising environmental impact.
The facility uses a modular design, so instead of building massive, centralised plants, it deploys small, modular units that can be easily scaled and adapted based on requirements. This flexibility allows for the recycling of batteries where they are discarded, eliminating the logistical challenges and environmental hazards of transporting used batteries across borders.
Read: How giant batteries can speed up South Africa’s energy transition
Each modular unit has the capacity to process a certain volume of batteries, but the design allows for future expansion. “We envisage many of these small-scale plants throughout Southern Africa and beyond,” said Cwenga Lib director Jenny Falconer.
Cwenga Lib’s focus is on cobalt-containing batteries, also known as NMC (nickel, manganese, cobalt) batteries, but plans are under way to expand the process to handle all lithium-ion batteries, regardless of their chemical composition. This broader capability will be essential as the industry shifts towards new battery technologies with fewer cobalt components.
The growth of the electric vehicle market is driving demand for lithium-ion battery recycling. Legislation in the EU now mandates that by 2031, at least 16% of the cobalt used in batteries must come from recycled sources, with this figure rising to 26% by 2036.
To minimise its environmental footprint, Cwenga Lib has adopted green practices. The chemicals used in the recycling process are reused and are apparently inherently safe. Additionally, the process is designed to operate with minimal water usage. Liquid waste that cannot be reused is managed responsibly by a third-party waste company, though these volumes are small compared to the hazardous waste diverted from landfills.
Read: South Africa faces lithium battery recycling headache
Furthermore, the facility has avoided energy-intensive methods like pyrometallurgy, which not only pose safety risks for workers but are also less feasible in regions like South Africa, where energy costs are high.
As demand for recycled materials grows, particularly with the rise in demand for EVs, the facility plans further expansion. Soon it expects to deploy between five and 10 modular units across South Africa and it may also expand later into neighbouring countries. – © 2024 NewsCentral Media