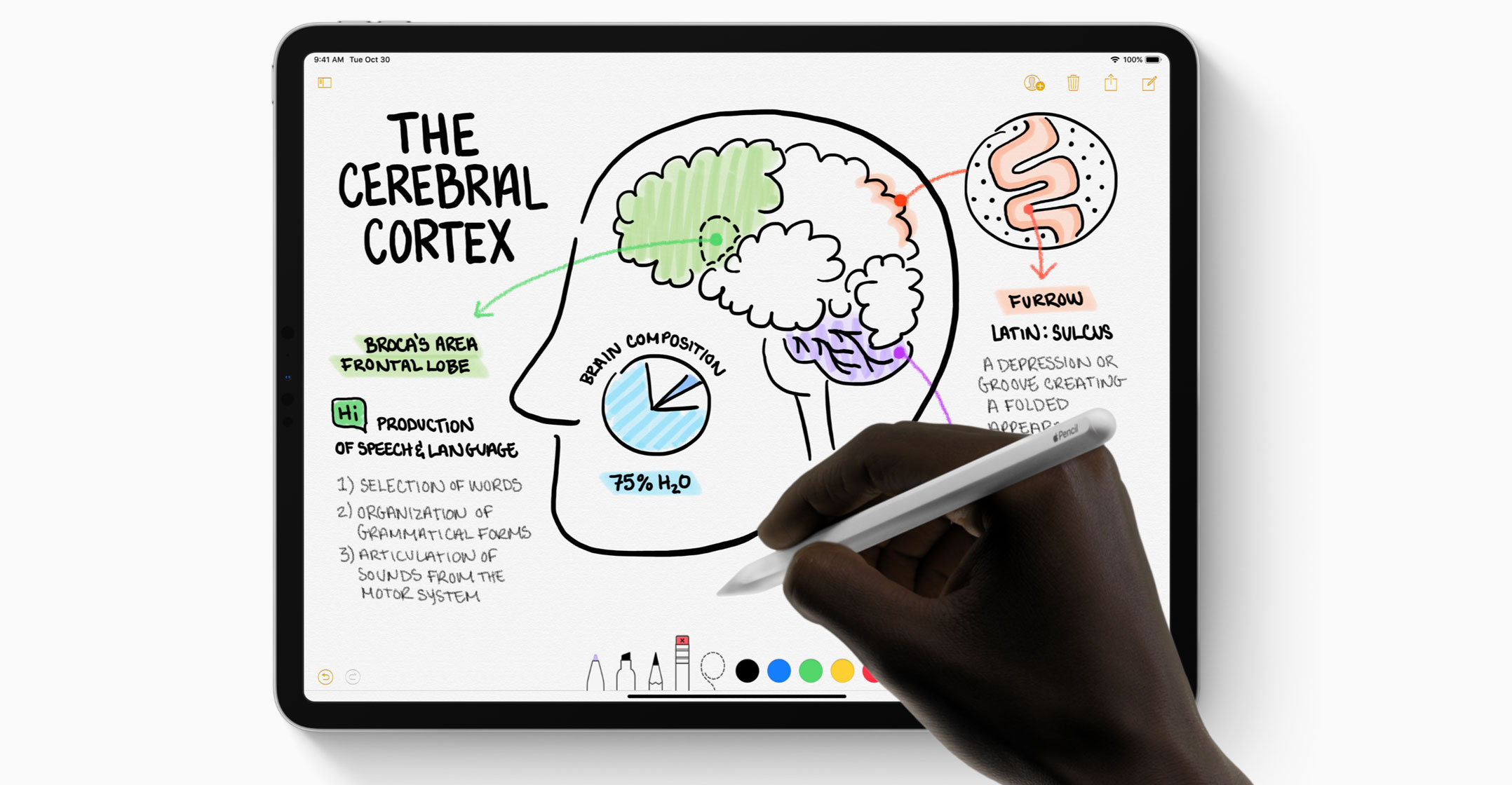
Apple kept its business rolling through the coronavirus pandemic this week by launching a new iPad Pro and two new Macs. But that doesn’t mean its supply chain is in the clear.
Deliveries of the new products will begin arriving on doorsteps next week. However, production of those devices likely started in early January, before the worst effects of China’s virus lockdown in February, according to people familiar with Apple’s supply chain.
With a fresh round of supplier factory closures enforced by Malaysia, and the virus disrupting operations in much of the rest of the world, the iPhone maker’s supply chain has not fully recovered yet.
Apple’s next flagship iPhones, with 5G wireless capabilities, are still on schedule to launch in the spring, although that’s partly because mass production isn’t due to begin until May, said the people. They asked not to be identified discussing private supply chain issues.
“Even as China comes back on line, we are beginning to wonder if Covid-19 will impact other supply-orientated geographies,” Brad Gastwirth, chief technology strategist at Wedbush Securities, wrote in a recent note to investors. “While China is improving, the supply chain for the electronics industry may yet see substantial disruptions.”
An Apple spokesman declined to comment. CEO Tim Cook, the architect of the company’s China-focused supply chain, said on 28 February that production issues would be a “temporary condition”.
Apple’s assembly factories in China, run mainly by Hon Hai Precision Industry, were in low gear for much of February. The manufacturing giant, also known as Foxconn, hopes to begin operating normally by the end of March.
Constraints
The February slowdown led to iPhone and AirPods supply constraints, but those have begun to subside. This week, Apple has been limiting iPhone purchases to two per customer on its online store in several countries. In early March, the company warned retail employees about shortages of replacement iPhones.
One new product unveiled this week suggests there’s strain on Apple’s supply chain, but also shows the company can still mass-produce gadgets given enough time. The keyboard accessory for the iPad Pro was announced Wednesday but goes on sale in May, an unusual delay.
Mass assembly is only one part of Apple’s supply chain. The company and its many partners spend months or years sourcing individual components that are assembled into final products. Any disruptions in this complex network could slow the introduction of future devices.
One person who works in Apple’s supply chain said not all operations are moving at normal speed because the flow of components to assemble is still slow. It will take another month or more to get parts moving steadily through the system, the person added.
Jabil, which makes iPhone casings, recently said its factories in China were “near normal”, while plants in other parts of the world were running 5-10% below capacity.
“Most of that is due to supply chain issues. In some odd way, as we sit today, I think China is the least of our concerns,” CEO Mark Mondello told analysts during a 13 March conference call. “We’re able to accommodate all of the demand that’s in front of us as long as we can get parts.”
A two-week lockdown in Malaysia is affecting several key suppliers that have operations in the country. Murata Manufacturing, Renesas Electronics and Ibiden, which make chips and circuit boards for Apple, have halted production there.
Micron Technology, which makes memory chips for Apple devices, is also impacted, but said an exemption allows “limited semiconductor operations to continue”. Texas Instruments and On Semiconductor have facilities in Malaysia, too.
Apple has suppliers and operations in other countries that have been hammered by the virus, including Italy, Germany, the UK and South Korea.
Samsung Display and LG Display make iPhone screens in South Korea, while many Apple engineers working on cellular modems are based in Munich, Germany. Apple also operates former Dialog Semiconductor facilities that work on power-management chips in Livorno, Italy, Nabern and Neuaubing, Germany, and Swindon, UK.
Virus impact
Apple has several hundred research and development engineers for future processors and underlying technologies in Israel, which is only letting citizens leave their homes for essential reasons, like buying food and medicine.
In the US, Apple has suppliers such as Corning for glass, and Qorvo, Skyworks Solutions and Broadcom for wireless chips. Broadcom CEO Hock Tan said recently that the virus “is going to have an impact on our semiconductor business, in particular in the second half of the fiscal year”.
Chips take months to make and test, and companies build up months of inventory. That means Apple and other device makers may not have seen the worst of the disruptions yet.
The virus is likely challenging Apple’s ability to design and test early versions of future products in Silicon Valley, which is grappling with a shelter-in-place mandate. The company has instated a remote work order, save for some mission-critical employees, for all its offices outside of China.
These struggles have yet to severely derail the 5G iPhone launch in the spring. During China’s factory shutdown in February, Apple was able to build a limited number of test versions of the new models, one of the people familiar with the company’s supply chain said.
Apple finalises the majority of design features for new iPhones between November and December of the year prior to launch, the people said. It begins mass-producing new casings around April and then starts a late manufacturing stage called Final Assembly, Test and Pack in about May.
Should Apple be unable to send full teams of engineers to China factories to finalise designs and resolve issues, this typical timeline could still slip, another person familiar with the company’s supply chain said. — Reported by Mark Gurman and Debby Wu, with assistance from Ian King, Yuki Furukawa and Gao Yuan, (c) 2020 Bloomberg LP