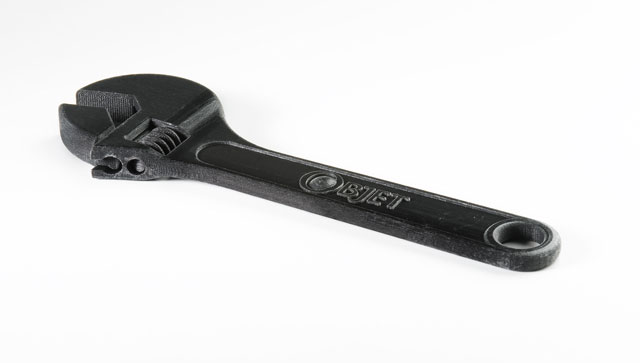
In a nondescript office park northwest of Fourways in Johannesburg, a printer was whirring away. But this was no ordinary printer. The Connex model from Israeli firm Objet Geometries is a 3D printer that jets a range of materials simultaneously to create 3D models.
When TechCentral visited local Objet distributor DemaPlasTech, the R2,2m printer was humming away industriously, building a fully functional fitting for a garden tap (see video below).
If the proponents of the technology are right, 3D printing could herald a revolution in the way the world makes things. And, in time, 3D printers could be as commonplace on people’s desks and inkjet and laser printers are today.
The Economist, in an April cover story, suggested that 3D printing, also sometimes referred to as additive manufacturing, would lead to the digitisation of manufacturing and bring about the third industrial revolution.
“The old way of making things involved taking lots of parts and screwing or welding them together,” the magazine wrote in a leader. “Now a product can be designed on a computer and ‘printed’ on a 3D printer, which creates a solid object by building up successive layers of material… In time, these amazing machines may be able to make almost anything, anywhere — from your garage to an African village.”
DemaPlasTech director Jacques Kleynhans says 3D printing technology has been around, in the form of rapid prototyping, for nearly 20 years but it’s only now starting to become mainstream as the technology improves and as prices fall. Basic 3D printers, which produce low-resolution 3D prints, are available for as little as R10 000. Higher-end devices, like Objet’s Connex range, which are meant for use by large companies, can fetch millions.
The Connex printer seen by TechCentral this week has eight print heads and can print from more than one cartridge, with more than 100 source materials available.
Kleynhans explains that the applications for 3D printing are almost limitless. “It’s applicable to any industry that wants to do fit, form and function testing,” he says. “If you take a computer-aided design, or whatever you’ve designed, be it toys, consumer goods, packaging or engineering goods, you can create prototypes and, in some rare instances, final product.”
In the past, he says, if a plastic bottle manufacturer wanted to create a new bottle design, it would typically cost tens of thousands or even hundreds of thousands of rand and months of labour to produce factory samples. With 3D printing technology, a prototype bottle can be printed within a matter of hours and changes made equally rapidly.
Although traditional manufacturing will still be used to produce the bottles in mass, creating prototypes in a printer ensures the product gets to market cheaper and quicker. Excluding the cost of the actual printer, producing a prototype bottle in a 3D printer costs only a few thousand rand.
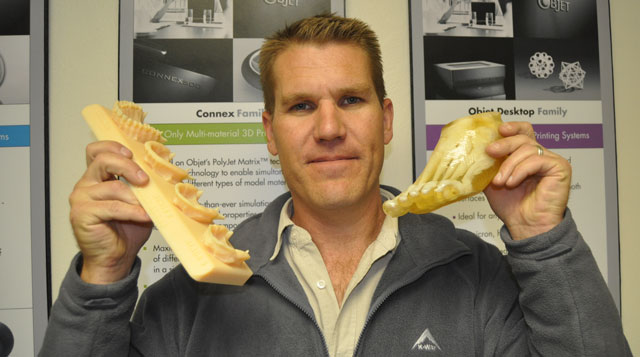
Another application could be in car manufacturing, where companies could build prototype automotive parts and test these thoroughly before putting them into production. “Image a manifold for water – you can print it, check that the clips work and that the hoses fit. You can quickly verify the design before going into manufacturing.”
Kleynhans says German sports clothing manufacturer Adidas has 10 3D printers that it uses to test shoe designs. It uses the system like a “3D fax machine”. It creates designs in software, encrypts the files and e-mails them to its offices around the world. “The very next day, they all have a physical sample of the shoe,” he says.
“The product development cycle has come down substantially, which means you can get to market quicker and start selling quicker,” he adds.
The technology can also be used for testing consumer products. New toy designs, for example, can be printed and given to a room full of three-year-olds. The toys they take a keen interest in are the ones that are likely to succeed in the market.
Some industries are even using 3D printers to produce final product. Dental laboratories, for example, have started using it to do away with the need for silicone moulds and other casts. “Now, dentists can scan your mouth digitally using a pen-shaped scanner, send the file to the lab, where it prints a model with the tooth and without it. They design the whole tooth digitally and nothing is done by hand.”
Another application is in printing hearing aids. Because everyone’s ear is shaped differently, it makes sense to use 3D printing to create them, complete with the necessary holes for the electronics.
Hobbyist market
Most computer-aided design and manufacturing software is able to read and manipulate the files — typically Standard Tessellation Language (STL) files — to create 3D prints. STL files are loaded into printing software, which then works out the best orientation and “cuts” the print into slices and sends those slices to the 3D printer, which then builds the output by depositing materials in thin layers until a product is created.
Kleynhans says Objet used its first range of 3D printers, called Eden, to print all of the prototype parts for its subsequent 3D printers. “It used its own machines to build its own machines,” he says.
The next frontier, Kleynhans says, is the home and hobbyist market, where people may want the ability to build parts that are not readily available. Objet doesn’t play in this space, but a growing number of companies are focusing on it, typically with fused deposition modelling technology. “If you’re not worried about having the greatest finish or resolution, then the result isn’t bad.”
There’s already a keen hobbyist market developing, with thousands of free 3D models available to consumers via websites such as Trimble SketchUp, which was previously owned by Google. People can download STL files and literally print the products in their homes. — (c) 2012 NewsCentral Media