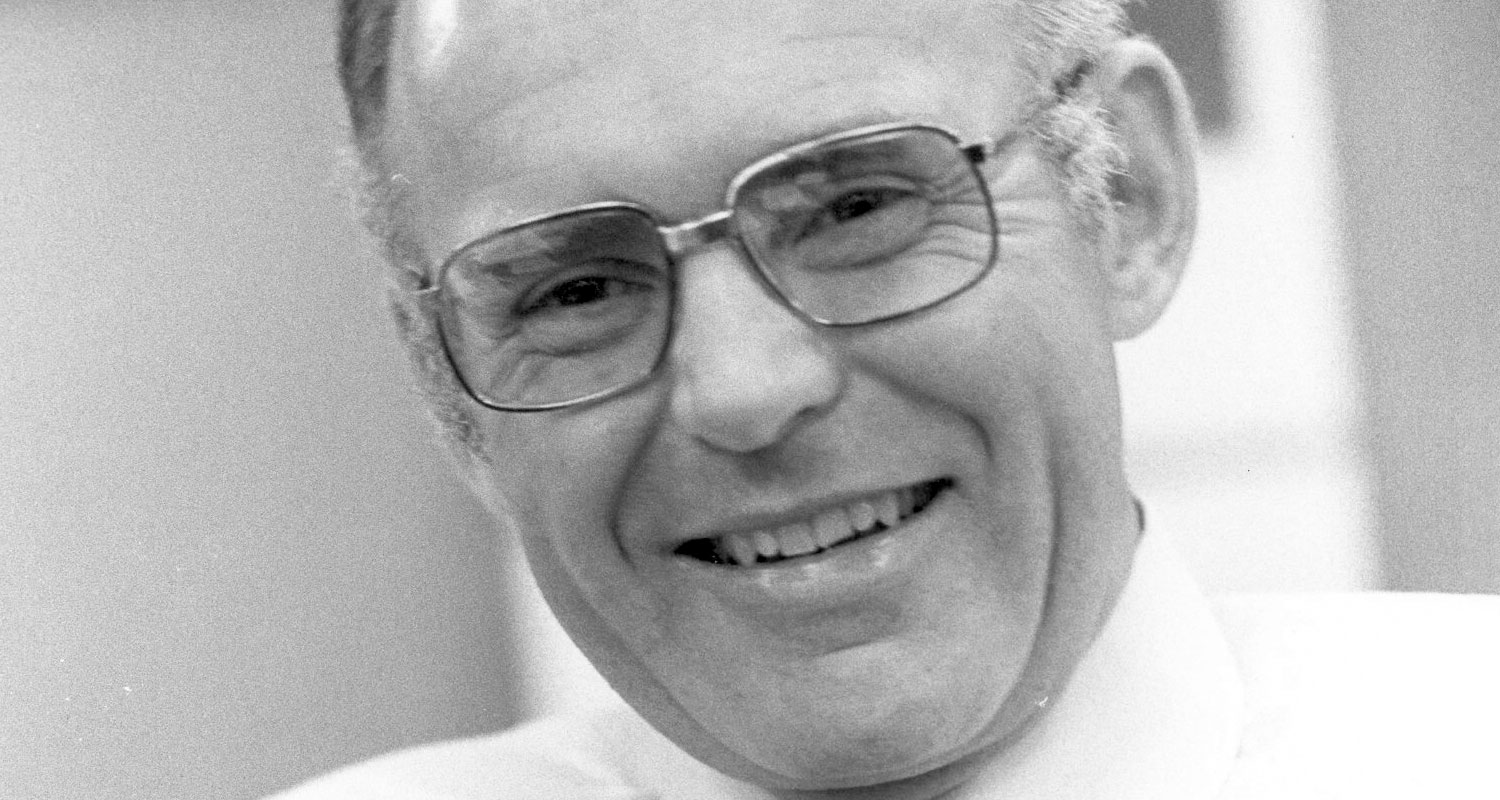
“Cramming more components onto integrated circuits.”
That was the blunt title of Gordon E Moore’s essay on silicon chips published in Electronics magazine in April 1965. In the space of just three pages, the director of semiconductor R&D at Fairchild Camera and Instrument outlined one of the most powerful observations in modern business and science. He wouldn’t have known it at the time, but it also serves as a precept ensuring semiconductor leaders stay ahead for as long as they keep spending.
Later dubbed “Moore’s Law” by noted scientist and engineer Carver Mead, that paper in the early days of electronics posited that the number of components per integrated circuit would double every two years. Moore, who went on to found Intel, expected it would be the case for at least the following 10 years. Almost six decades later, it still holds true.
There’s almost no other sector in history that’s shown the same level of consistent development for so long. Cars are little faster than they were in 1965, although fuel economy almost doubled in that time. Battery technology, key to the future of electric vehicles, saw an even more impressive 40-fold improvement in cost per kilowatt-hour between 1991 and 2018.
Since Moore’s prescient remarks, the number of transistors per chip has increased from 100 to almost 50 billion while the size of components has shrunk. In simple terms, the density rate added a zero every 3.5 years. Moore published his original prediction as a logarithmic chart of base two, but in standard notation it looks more like a hockey stick.
An important implication of this trend is that the cost of computing plummeted. Chips work by feeding binary units (bits) of data into logic gates in various combinations, with the output giving the result of the calculation. More gates mean a faster rate of computation, offering more powerful uses. Among the earliest was the deployment of chips to sense a target and calculate a trajectory in missile guidance systems during the Vietnam War. It’s well-known that an iPhone today packs a stronger punch than a room full of circuits in 1970, and for much less money.
Harder to make
But around a decade ago, that started to change. As semiconductor analyst and writer Doug O’Laughlin pointed out, the price per gate plateaued and then began climbing from the 28-nanometre node. That technology was unveiled by Taiwan’s TSMC in 2011, with rivals including United Microelectronics following in subsequent years.
The reason is simple: semiconductors are getting prohibitively harder to make. TSMC’s spending on equipment rose 74% last year to $30-billion, yet its shipments — measured in 12-inch wafers — climbed a mere 14.8%. While Moore’s Law offers more transistors, the cost escalations outweigh the density benefits. This year, TSMC will spend more than $40-billion.
These climbing costs are a major reason manufacturers have dropped out of the competition. In the early years Motorola and AMD were major names. Not anymore.
But there’s a slew of Chinese companies coming forth. Some are seasoned veterans like Semiconductor Manufacturing International (SMIC), and others more fresh on the scene, such as Yangtze Memories Technology. With Beijing’s backing, both political and financial, China’s chip sector has spent untold billions trying to catch up with Taiwan, South Korea and the US. They’ve largely failed.
Although much has been written recently about Chinese advancements, the analysis often forgets that the rest of the sector is also moving forward. There’s good reason to be sceptical of claims that SMIC recently produced chips at the 7nm node, a big leap forward for the country’s leading chip maker. How many chips it produced, and at what level of accuracy (yield), are key to assessing whether this was a legitimate breakthrough or a lucky break. Yet, even if we take this news at face value, we can still conclude that China hasn’t gained on leaders like Samsung Electronics and TSMC.
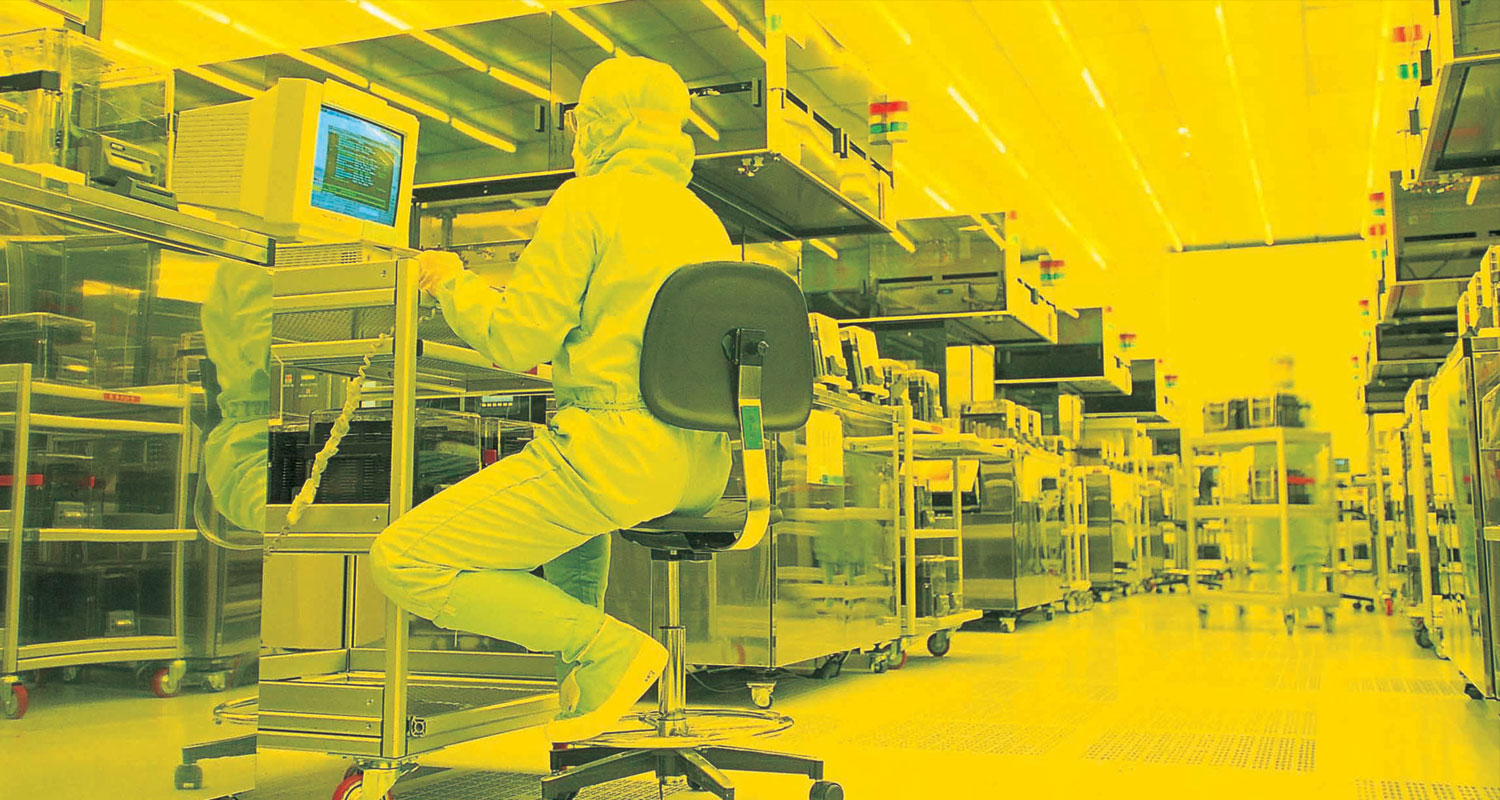
In fact, when SMIC announced its move to 28nm production, it was three years behind TSMC. Now, SMIC’s small output of 7nm chips comes four years after TSMC released the technology into mass production.
The rising costs of semiconductor manufacturing (at $10-billion per factory), the increasing complexity of modern techniques, and more intense R&D required just to operate new equipment, makes it easy for a company to fall behind. On the flipside, however, money alone is not enough to make up ground. That’s because of Moore’s Law.
Once a leader such as TSMC, Samsung or Intel announces their transition to the next node, the race is on for everyone else to catch up. Rivals have been known to beg, borrow and steal information to close that gap. Even then, it takes years to work through the myriad manufacturing steps required to make a chip. And in that time, the leaders aren’t sitting still. A new breakthrough merely restarts the two-year timer before they’re expected to, and usually do, deliver the next manufacturing node.
China’s latest tactic is to try to leapfrog the leaders with entirely new chemical engineering processes that scientists hope will give them a revolutionary breakthrough. So far, that big risk has yet to pay off. Intel, too, is hoping to retain its tenuous grip on semiconductor leadership by speeding up the pace of development.
Even as Chinese chip makers work hard to catch up, Intel, Samsung and TSMC are still racing ahead. The Taiwanese foundry last year spent $4.5-billion on R&D, seven times more than SMIC. The American giant outdid them both, spending $15.2-billion. In the end, spending merely allows leaders to remain in the game. It’s Moore’s Law that keeps them ahead of the pack. — (c) 2022 Bloomberg LP