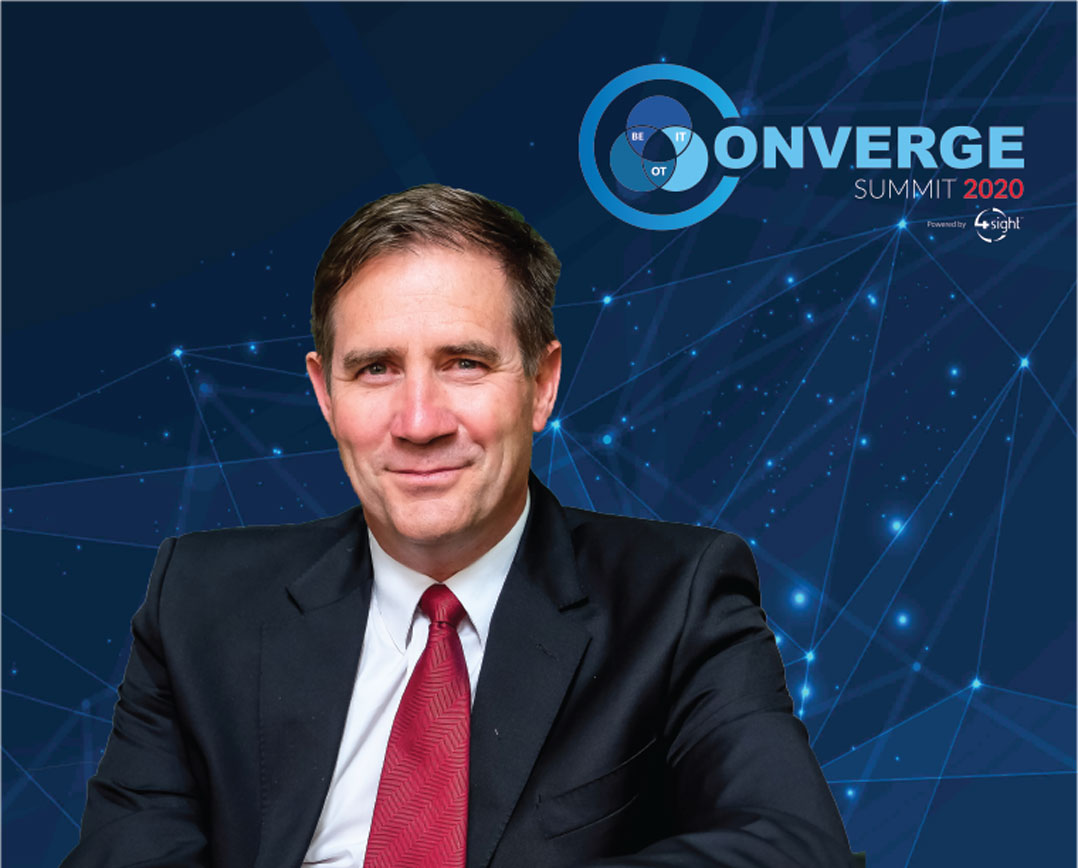
The fourth Industrial Revolution (4IR) will use emerging technologies like the Internet of things, artificial intelligence (AI), machine learning (ML), robotic process automation, 3D printing and the like to revolutionise businesses of all kinds.
However, the benefits of the 4IR will only be fully realised by the Enterprise 5.0 organisation. The next-generation Enterprise 5.0 organisation will be powered by its ability to integrate IT, operational technology (OT) and the business environment to create a rich data store that supports a step change in efficiency and productivity, and hence higher levels of profitability.
Some of the biggest opportunities lie in the OT environment, which covers all the systems, equipment and machinery used in mining, manufacturing, logistics and warehousing, and energy generation. In the emerging Enterprise 5.0 organisation, the data from these systems is integrated with the data from the IT systems to maximise business benefits.
Let’s explore the opportunities within OT in a little more detail.
In the “real” economy, businesses use a wide range of equipment and vehicles to create and deliver their products to clients. In these complex supply chains, the performance of the individual pieces of equipment and machinery is vital; equally vital is the way they integrate into a web of interconnected processes to produce, market and distribute the final goods.
Much of this equipment, particularly in mines and manufacturing plants, has always had a range of sensor-based control mechanisms (programmable logic controllers) and manufacturing execution systems. But these operational technologies have typically operated to a greater or lesser extent in isolation.
What Enterprise 5.0 means
Increasingly, they are being connected to the corporate network, but few have properly begun to realise the full Enterprise 5.0 scenario. Enterprise 5.0 means aggregating the OT data with the data from the business systems (IT) in the cloud. There, using AI and ML and harnessing the processing power available in the cloud, the huge amounts of data can be analysed within the context of the entire process to uncover beneficial insights.
The cloud is critical to Enterprise 5.0 because it provides the platform where the large amounts of data can be aggregated and, crucially, processed. At present, the typical organisation focused on operational technologies only uses around 4-8% of its data; in Enterprise 5.0, the aim is to use it all.
For example, this kind of analysis can be used to optimise an organisation’s expensive assets by identifying trends hidden in historical data to predict when a machine will need to undergo maintenance in order to prevent the unexpected breakdowns that impact the entire process, often dramatically. We have helped clients improve the availability of their assets by 25%, and reduce the delay time by 40% and maintenance costs by 20%.
Known as asset performance management, this kind of solution can save a company huge amounts of money.
This kind of integrated data analysis can also be used to improve workplace safety by up to 20%, and energy efficiency can be improved by up 20% while reducing the carbon footprint by a similar amount.
Seeing through process complexity
As noted above, these individual pieces of equipment or machines all fit together within a complex web of processes, a universe of interlocking variables that interact with each other in a multitude of ways. The massive computing power available in the cloud can be used to visualise these variables within the context of the process to predict outcomes and, by creating digital simulation models, to optimise not only each process but how the disparate processes work together (advanced process control) and to improve overall equipment effectiveness. In short, the crippling effect of variability can be tightly managed to improve outcomes, underpin efficiency and bolster profits.
One global mining company was able to use this approach to optimise the efficiency of its coal-fired boiler. Steam pressure variability was reduced by 50% while enabling a reducing in coal usage of 7.27%, thus improving the efficiency of the boilers. The company not only made the boiler more efficient; it also made the process more environmentally friendly.
In similar vein, another mining company was able to leverage powerful data analysis to optimise a complex lead zinc flotation process by manipulating 23 variables. The number of reagents using in the process was able to be reduced substantially—copper sulphate by 23% and ethyl xanthate by 38%. Using lesser amounts of these expensive chemicals contributed to a significant reduction in overall costs.
The power of the incremental approach
As can be seen, the integration of OT with IT and the business environment can generate substantial savings while enhancing process efficiency. Equally important, though, is the fact that these improvements can be realised incrementally, step by step. This means that the cost and efficiency savings from each project can be used to provide at least partial funding for the next one until the full Enterprise 5.0 model is put in place.
In conclusion, we must take into account the current context, in which the Covid-19 lockdowns are driving rapid digitalisation. Cloud and data-focused implementations for OT projects are in demand because they provide new ways of managing sites remotely to minimise people on the ground. The trick now will be to use the resulting torrent of data intelligently to help the organisation remain profitable in what is an increasingly volatile, uncertain, complex and ambiguous world. Only the Enterprise 5.0, with its integrated approach to using all its data to drive productivity and responsiveness, has the capacity to navigate these treacherous waters.
For more information about how 4Sight is assisting industrial and mining companies, please register for Converge Summit 2020 on 22 October 2020. Go to www.registertoday.co.za (attendance is free).
- Wilhelm Swart is chief OT officer at 4Sight
- This promoted content was paid for by the party concerned